HÖRMANN Automotive develops chassis inspired by the natural world
The new integral chassis concept for lightweight commercial vehicles from HÖRMANN Automotive GmbH features an oval topology reminiscent of a nut or a tortoise, making it safe and yet light at the same time for its application protecting the energy storage unit. In terms of manufacturing technology, the concept builds on the findings of the Technical University of Darmstadt’s Collaborative Research Centre (SFB) 666, a project dealing with integral sheet metal design with higher-order bifurcations and the development, production and analysis of such products. This uses the technologies developed as part of the project in a vehicle manufacturing application for the future of urban delivery logistics. It uses the bifurcated sheet structures to implement new mechanisms for protecting energy storage units in vehicles with alternative drive systems.
‘For the purpose of production research, implementing findings from academic research in industrial pre-production and series production development projects is immensely important in ensuring coherence between university research and the topical challenges of industrial production,’ said Professor Peter Groche, head of the Institute for Production Engineering and Forming Machines (PtU) at TU Darmstadt and a former spokesperson for SFB 666.
‘During development of the chassis, we took inspiration from the natural world,’ said Wolfram Schmitt, head of central research and development at HÖRMANN Automotive GmbH. ‘Studies have shown that when used in vehicle chassis, oval structures can exhibit more favourable behaviour in a collision than rectangular structures. Some plants and animals also use oval shapes to give extra protection to their inner workings. We are using the same mechanism to protect energy storage units in the chassis of vehicles with alternative drive systems. That is allowing us to reduce the complexity of systems currently used for protection, such as battery boxes. Equipped with the research findings from SFB 666, we were able to implement the original idea in an innovative and yet also financially reasonable manufacturing and material strategy.’
Co-operation with TU Darmstadt and DLR
Overall chassis development took place in a network including PtU at TU Darmstadt as well as the German Aerospace Center (DLR). This co-operation allowed topological optimisation to validate the original idea for the oval shape. Actual implementation in a production context involved working closely with production researchers at TU Darmstadt.
Non-linear multi-chamber profiles made of steel were developed in accordance with the basic topological idea and using the methods and forming processes devised in SFB 666. These ensured that the internal energy storage unit was protected by taking the opportunities presented by load-adaptive design. ‘The findings obtained in SFB 666 have been put to exemplary use in the longitudinal member of the integral chassis because the forming mechanisms of linear flow splitting are used not only to create the integral bifurcation but also to shape the high-strength profiles. This combination makes the bending process easier and allows for much better forming accuracy for the bifurcated, non-linear structural components than was the case with previous technologies,’ said Groche.
The resultant approach to efficient lightweight structural design yields financial benefits and offers extremely promising prospects for the future, particularly given the systematic move towards fitting light commercial vehicles with alternative drive systems. PtU at TU Darmstadt and HÖRMANN Automotive GmbH intend to continue working on this area beyond the presentation of the concept vehicle at the 2018 IAA Commercial Vehicle Show. ‘Ultimately applying the findings from our research to industrial processes is one of the main goals behind our efforts. That’s why I’m so pleased that the integral chassis concept from HÖRMANN Automotive gives us an ideal example of how our twelve years of research can be translated into a production-ready application,’ said Groche. Thomas Vetter, managing director of HÖRMANN Automotive GmbH, added, ‘In an era of growing urbanisation combined with the threat of city-centre vehicle restrictions due to the impact of carbon dioxide emissions, we need to find solutions – especially for future urban delivery logistics. Our collaboration with TU Darmstadt represents a huge step in the right direction.’
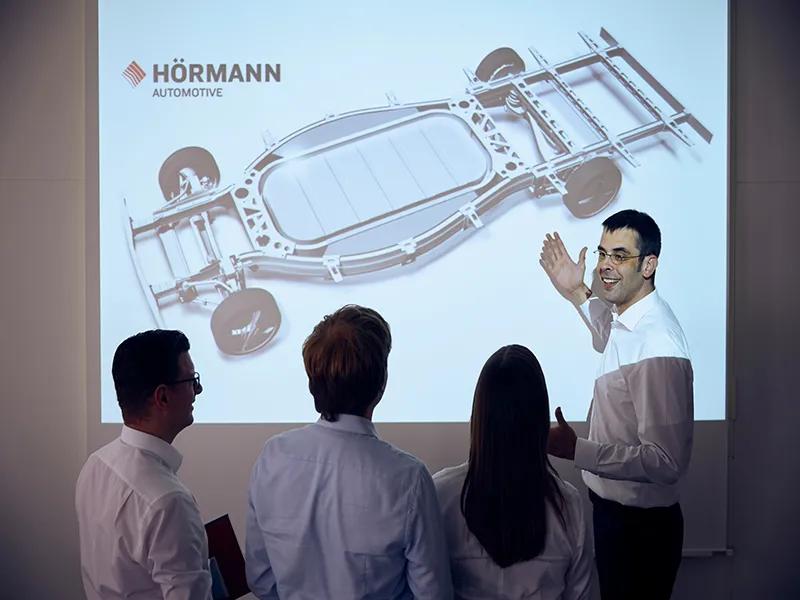