MAT Maschinentechnik provides machinery relocation services from a single supplier
The process of relocating machinery and systems presents major challenges for many companies. From planning to logistics all the way to actual execution, they often lack the necessary personnel resources or technical equipment. Even moving a machine within the company can therefore quickly become a difficult task. This is where a capable partner comes in. From machinery relocation as part of production changeovers, relocating complete manufacturing systems and production lines or even entire plants, MAT Maschinentechnik has been offering customers all the necessary services from a single supplier for more than 40 years.
In 2020, MAT Maschinentechnik relocated a system to a different factory to improve logistical processes for an OEM in the steel industry. ‘The customer chose to call upon our dependable expertise, having already commissioned us for a number of previous projects,’ said Gerhard Jacobi, managing director of MAT Maschinentechnik.
Machinery relocated without a hitch
Up through recommissioning at the new location, MAT Maschinentechnik can offer a customer all services in the areas of planning, disassembly and re-assembly, including loading and transport. This avoids misunderstandings and ensures a seamless operation that is supervised by the engineers from start to finish.
The process of relocating the system involved disassembling and re-assembling a milling machine weighing 320 tonnes and measuring 60 metres in length, including its infeed and outfeed conveyors. This equipment is used to machine steel plates weighing around 2.5 tonnes each. ‘The size of the system meant that it wasn’t exactly an everyday assignment for the team,’ said Jacobi.
Industrial services made to order
Once project planning and scheduling, data backup, assembly labelling, geometric machinery data recording and the installation site were all in place, it was time for the project to begin. The new energy container for supplying the system with the necessary electricity was designed, delivered and assembled at the new site, including climate control units.
The team members broke the system down into transportable units and loaded them onto 18 low-loader trucks so that they could be driven to the new location. Once they had arrived, precise measurements were carried out and mounting elements adjusted to fit the machinery. Re-assembly included positioning and aligning the machine, establishing the correct machine geometry, installing the infeed and outfeed conveyors and recommissioning the machine and the rest of the system.
‘Numerous electrical repairs were carried out on the system during relocation and recommissioning,’ said Jacobi. He added, ‘When older systems are relocated, various electrical components, such as cables that have been in use for a while, can sometimes fail as a result of the stresses and strains of transport. This adds an extra layer of difficulty to precise scheduling. Not only that, but the high weights and enormous dimensions of the assembles call for an extremely cautious approach to the loading and transport of the components.’
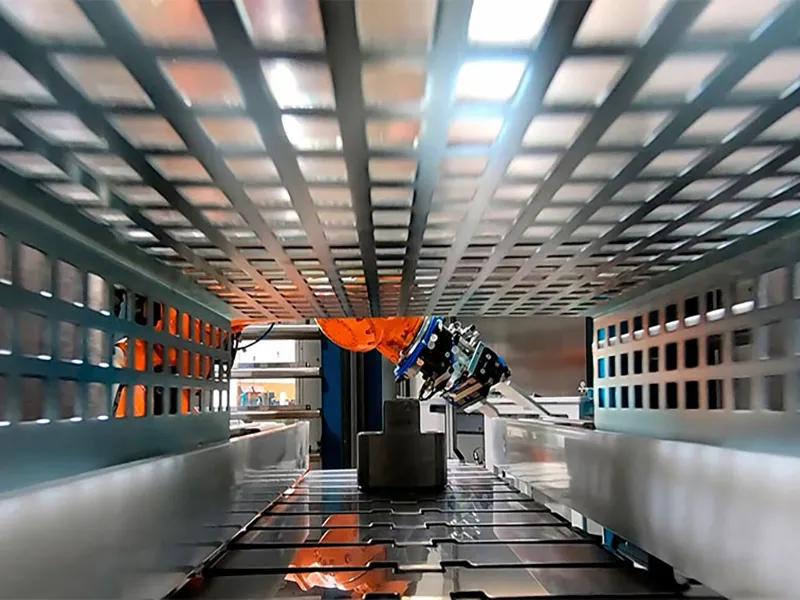
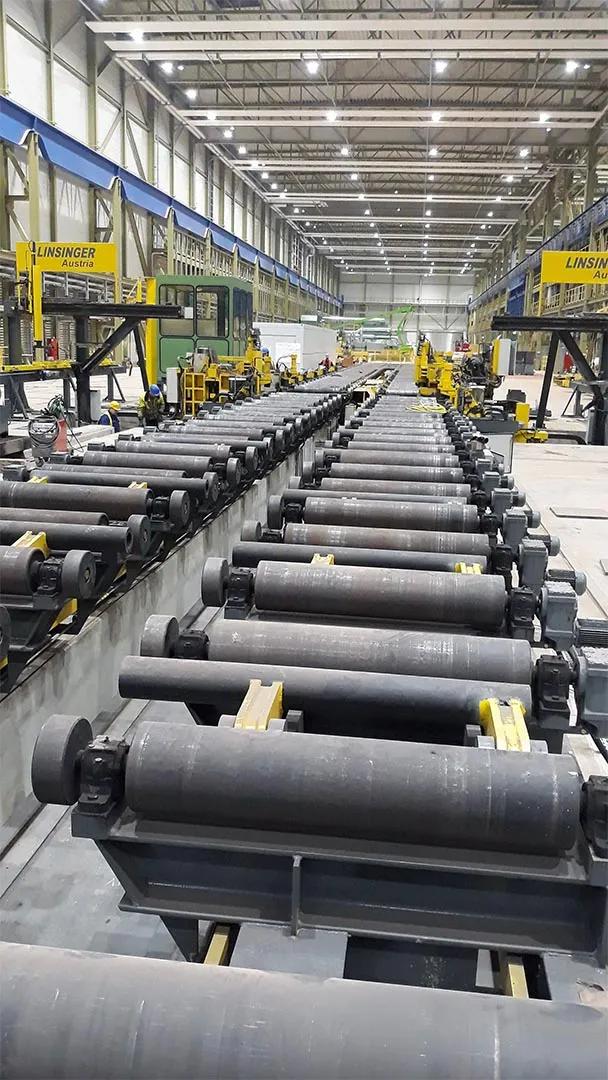