HÖRMANN Automotive broadens capabilities to include hot working and press hardening
HÖRMANN Automotive GmbH is an established and recognised expert in cold working on fine sheet metal for body-in-white parts and for all kinds of chassis components made from thick sheet metal, which are widely used in the assembly of light and heavy-duty trucks as well as in the agricultural and construction machinery industries. ‘However, certain component geometries and their properties can be produced only by means of hot working, and some components even require wear-resistant surfaces and press hardening,’ said Uwe Jung, managing director of the factories in St. Wendel and Saarbrücken.
The HÖRMANN Automotive factory in St. Wendel in the German state of Saarland has now made a significant new investment and broadened its technological capabilities to include the hot working and press hardening production processes, which have been integrated in an automated production cell and can handle blanks measuring 1,900 x 1,600 millimetres at throughput of 1,200 kilograms per hour. All system components, such as the blank lubrication system, annealing furnace and 800ton hydraulic press, are linked together. The entire handling process is performed by a number of robots, with automated operation ensuring high process reliability, top quality and first-rate efficiency.
Various technologically advanced components for agricultural machinery such as Claas forage harvesters and CNH combine harvesters are now produced on this system as of 2019. By adding to its technological capabilities with the future in mind, HÖRMANN Automotive is responding to growing demand for hot working and press hardening, both key technologies, and this investment has helped consolidating its already strong market position as a significant supplier to the European agricultural and construction machinery industries.
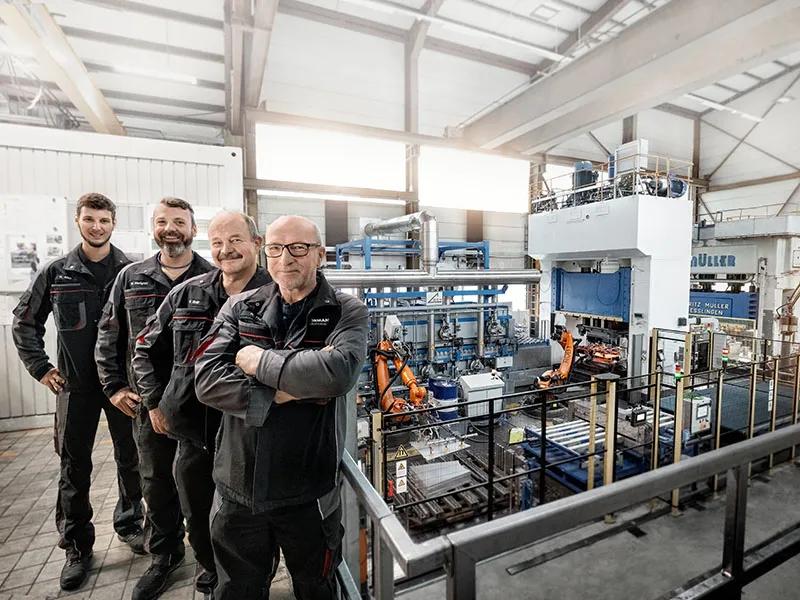
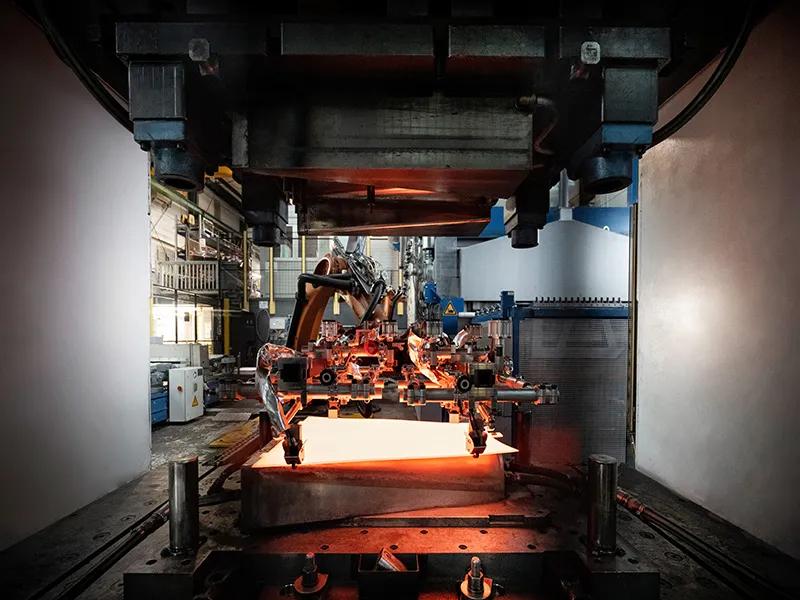