HÖRMANN Automotive helping to reshape agriculture amidst changes in technology
The scale of the changes to agriculture over the last hundred years is impressive. At the turn of the 20th century, when Germany was still largely an agrarian society, around 38% of the labour force worked in farming and forestry, and one farmer could feed around four people. Today, that first figure is just 1.8%, and one farmer feeds 135 people on average.
‘This enormous advance in productivity could not have been possible without the use of ever more efficient machinery, and that still applies today,’ said Uwe Jung, managing director of HÖRMANN Automotive in Saarbrücken and St. Wendel. One pivotal factor in production is the forage harvester. First developed in the 1940s, it is one of the most recent items of high-performance agricultural machinery.
Complex, high-quality components secure improvements in productivity
As the cultivation of maize became more widespread and agriculture underwent a process of rationalisation, the first self-propelled forage harvesters came onto the market in the 1970s. Initially, they had a working width of two metres and a power output of 102 metric horsepower; today, they can develop as much as 1,155 metric horsepower and cover ten-metre widths.
The customer on this project comes from the agricultural machinery industry and, selling around 800 machines per year, is one of the leaders on the global market. ‘Our customer manufactures the forage harvesters at its factory in Zweibrücken, roughly 30 kilometres from Saarbrücken,’ said Jung.
One particularly striking and technically sophisticated component on this equipment is the discharge spout because this is the section through which all the crops flow, which makes it absolutely essential to the performance of the machine. Two years ago, the customer decided to switch its discharge spouts from a conventional box design made from laser-cut sections and edgings to a welded system with pressed parts, its aim being to optimise functionality and thus the flow of crops.
Synergies found in discharge spout production
HÖRMANN Automotive in Saarbrücken secured the contract for this strategically important project in May 2020. ‘But that wasn’t all. The new design also includes deep-drawn components, so HÖRMANN Automotive in St. Wendel is contributing those parts. It’s an example of the two factories working shoulder to shoulder in a way that ultimately benefits the customer,’ explained Jung.
All in all, a next-generation discharge spout comprises 220 in-house parts, 160 purchased parts and 900 standardised parts, joined together using welding apparatus operated both by hand and by automated systems, with 500 welds adding up to a total welded length of 30 metres. At the end of this complex manufacturing process, the discharge spout is assembled, painted and delivered to the customer’s assembly line, ready to be installed.
‘By April of next year, we will be delivering 12 prototypes and 80 pre-production vehicles, then full-scale delivery will begin in November 2021 and we will hit peak production by 2024,’ said Jung. Getting the project off the ground and ensuring an efficient launch phase means tackling an array of assignments, such as a new system for the use of space, optimised value stream designs and the definition and documentation of production processes. On this matter, HÖRMANN Automotive can rely on the assistance of the factory planners at HÖRMANN Rawema, and can also make use of the synergies that come from being part of HÖRMANN Group.
‘We are very proud to be able to play an important part in helping to supply food to the growing global population thanks to our role as a reputable and long-established partner to the agricultural machinery industry,’ said Jung on behalf of his team.
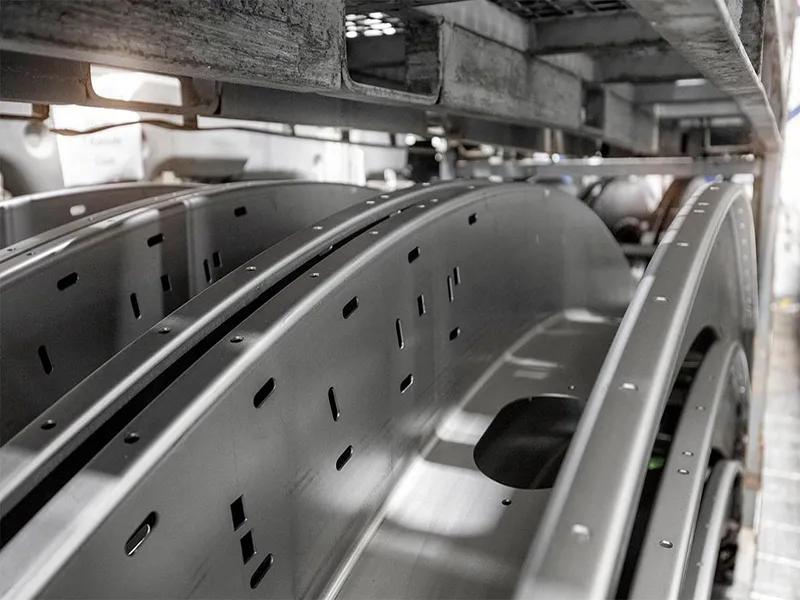
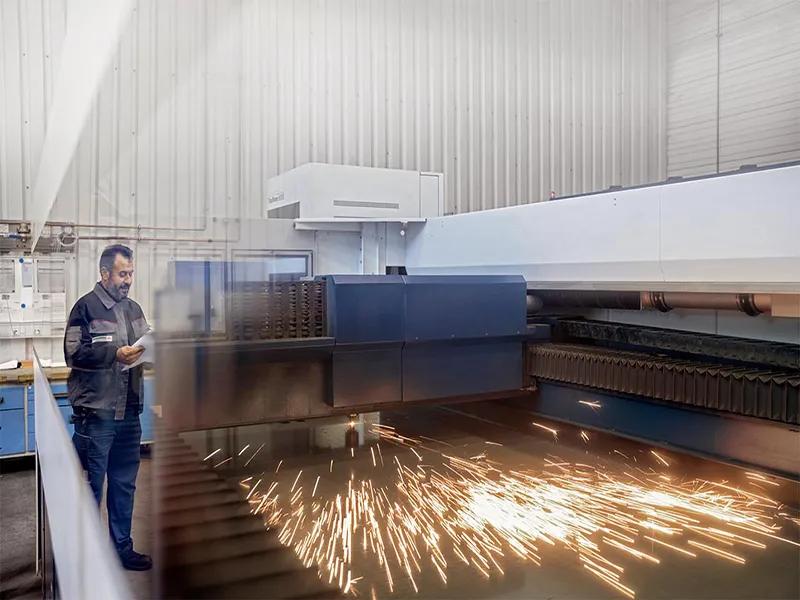