HÖRMANN Automotive offers high-performance handling of large vehicle body parts
Automating and increasing the performance of fine sheet press line 2 is a key focus for the HÖRMANN Automotive press shop in Gustavsburg. The production of large pressed fine sheets for structural parts and outer skins has been a core area of expertise for the company for many years. ‘We have invested in new technology to meet the challenges presented by our most recent new orders, such as side panels for light-duty commercial vehicles and driver cabs,’ said Andreas Müller, managing director of HÖRMANN Automotive in Gustavsburg.
One particularly tricky aspect associated with large fine sheets is handling them. The size of the parts and their relatively low thickness mean that handling them manually can easily have a detrimental impact on quality or cause problems with processes. That is why in 2018, the factory invested in a fully automated system for end-of-line stacking and packaging of the components on press line 2 to account for more exacting quality requirements on the part of customers. At the same time, this measure cut takt time significantly whilst also boosting efficiency. Since then, fine sheet parts have been automatically removed from the line by robots, packaged in customer-specific special load carriers and readied for shipment.
New feeder system for better efficiency
To make the entire manufacturing process even safer and more efficient, the process of transporting the large components between the presses has undergone something of a rethink as well. To improve performance, the experts at HÖRMANN Automotive worked with a team from NSM to develop a new feeder system that improves manufacturing speed and takt time by moving the components within the press unit more quickly.
This investment, prepared at the end of 2020 and commissioned early in 2021, is paying off in many ways. Because the presses are now linked not with two feeders and an intermediate storage position each as they were before, but instead with one four-axis feeder system each, the entire press line is more reliable, and component quality has been improved. ‘The upgrade to the performance of press line 2, increased system availability and improved component quality will enhance the Gustavsburg’s positioning for continued growth in the future as a supplier of large pressed fine sheets for outer skins and structural parts,’ said Müller.
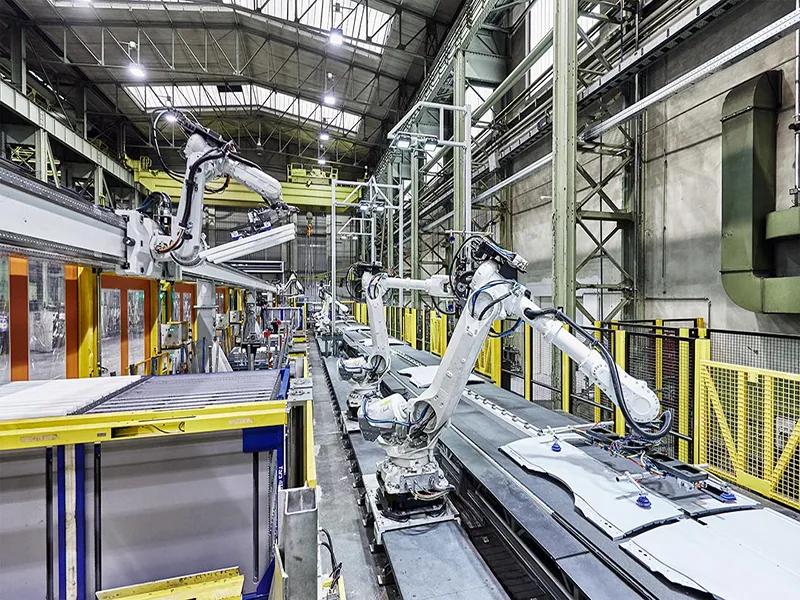
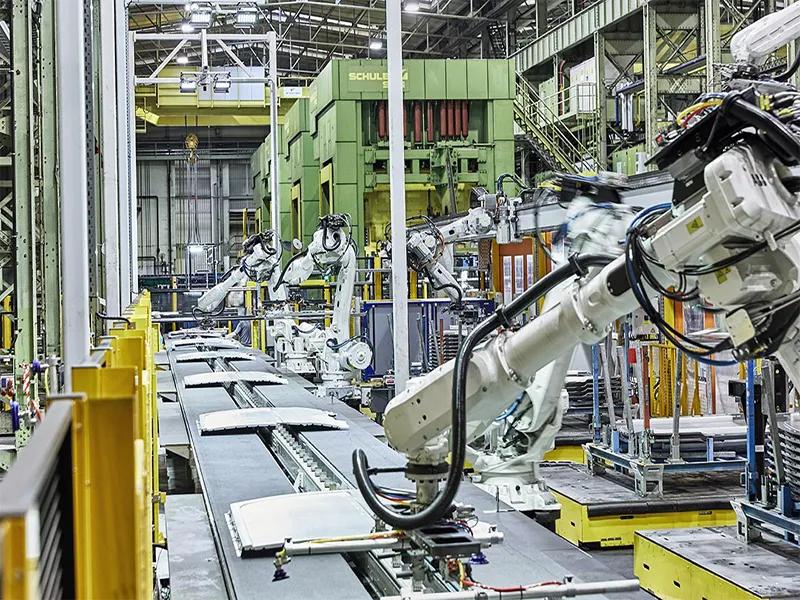