HÖRMANN Rawema’s smart factory nominated for Sächsischer Innovationspreis award
Digitalisation and direct information and communication channels, online and in real time, are changing the face of industrial production. Key concepts such as Industry 4.0 and smart factories refer to the resultant innovative and dynamic collaboration between humans and technology both within and between factories in a truly multifaceted way. The wealth of potential in place for businesses is matched by the ever-growing range of detailed and single-purpose solutions available on the market. Consequently, one crucial challenge factory planners at HÖRMANN Rawema are facing, lies in thinking logically to select the appropriate digital functions and harmonise data streams accordingly.
To draw a line between that and more generalised, wide-ranging concepts, the company developed a smart factory demonstrator that can be used to examine current tools from Industry 4.0 in an industrial setting and confirm their effectiveness and applicability. To maintain investment costs at a moderate level and keep the demonstrator mobile, a model production system was configured with a high-tech and low-cost strategy in mind. This system combines Lego bricks (e.g. conveyor belts, handling systems) and industrial components (e.g. laser machines, vibration/temperature sensors) via SIMATIC S7. Communication and the connection to the database take place via an OPC UA application. All transport and handling operations are fully automated. There are plans to expand the system further.
‘With our smart factory, we reached the top ten nominees for the 2019 Sächsischer Innovationspreis awards,’ said managing director Holger Füssel.
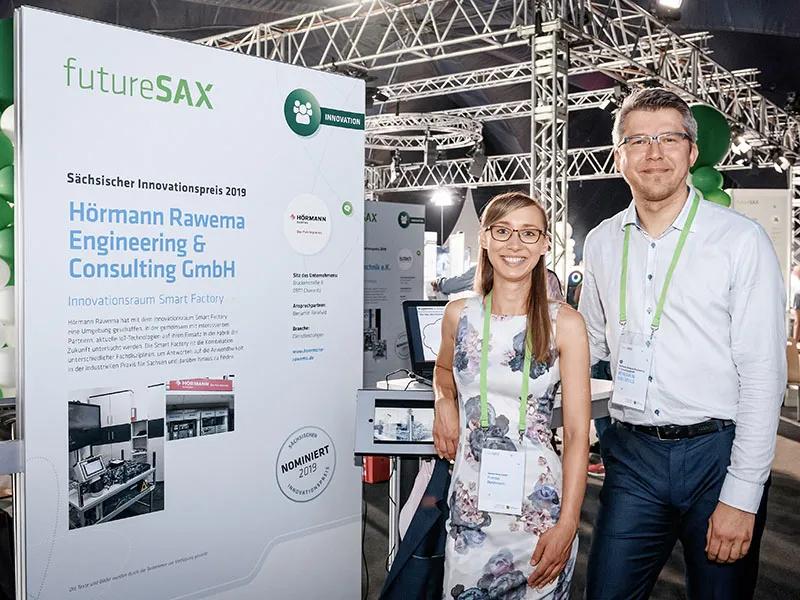