HÖRMANN Services offers reliability and perfect timing for transport through series production
Assembling a modern car with an internal combustion engine can require as many as 10,000 components produced on highly automated and precisely timed production lines featuring numerous workstations and a wide variety of manufacturing methods. Reliably transporting components from station to station at the right times is extremely important in maximising the efficiency of these production facilities, particularly given the millions of euros of investment that have been poured into them.
NTN Antriebstechnik GmbH, a subsidiary of the Japan-based NTN Corporation located in the town of Gardelegen in Saxony-Anhalt, is a world-leading producer of driveshafts for the automotive industry and a supplier to some high-profile German carmakers. In connection with the installation of two new production lines, NTN contracted HÖRMANN Services GmbH to link up the various workstations. This project involved some fairly ambitious targets, such as a line takt time of 36 seconds and an output of 800 components per shift.
HÖRMANN Automationsservices GmbH drew up the system layout, the mechanical link design and an automation plan, including an electrical plan. The linking process was built around the articulated chain conveyors and the loading stations, which are used to transport workpieces weighing up to 2.2 kg. One particular challenge involved in managing the project was integrating a tempering furnace for heat-treating the workpieces and using a lifting/lowering station to keep the path clear to move through production.
HÖRMANN Industrieservice GmbH, a sister company of HÖRMANN Automationsservices GmbH, installed the mechanical components, all safety equipment and the electrical apparatus.
The automation technology and in-house software ensure precisely timed management of the entire process of transporting items from station to station with a high level of availability, with each production line given its own controller with plenty of protective circuits. HÖRMANN Services also offers numerous product-related services such as inspecting electrical equipment for compliance with DGUV 3 regulations, training operational and maintenance personnel, commissioning the system, supervising the start of production and all the usual documentation, instruction manuals and maintenance schedules. Following several changes to the list of parts involved, the entire production facility successfully entered operations at the start of 2020.
Looking ahead to new challenges, Matthias Piofczyk, managing director of HÖRMANN Automationsservices GmbH, said, ‘This project gave us an opportunity to demonstrate the full capabilities of HÖRMANN Services – namely, turnkey automated production facilities entirely from a single supplier.’
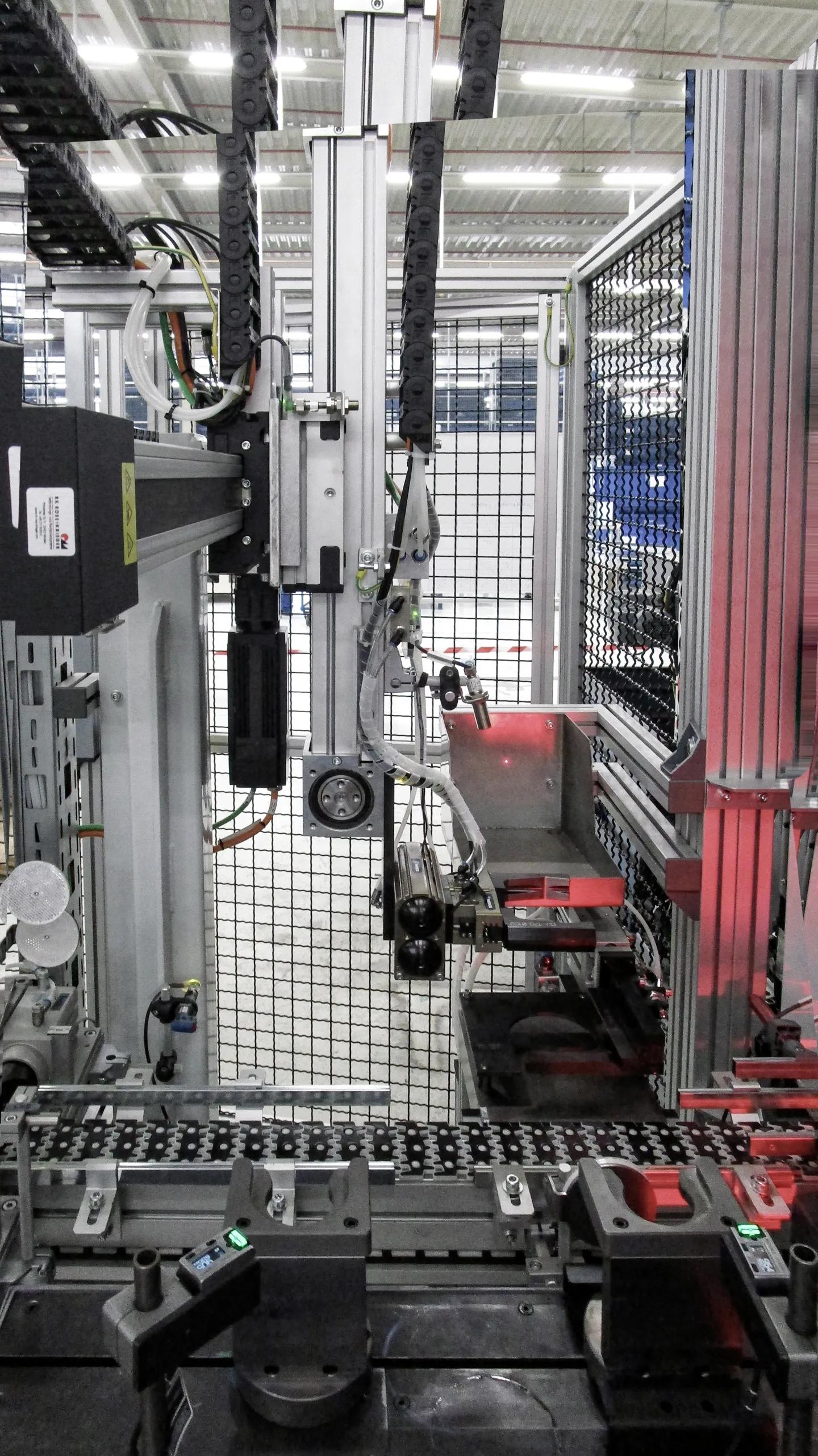